How to manage and reduce carbon emissions in new infrastructure projects
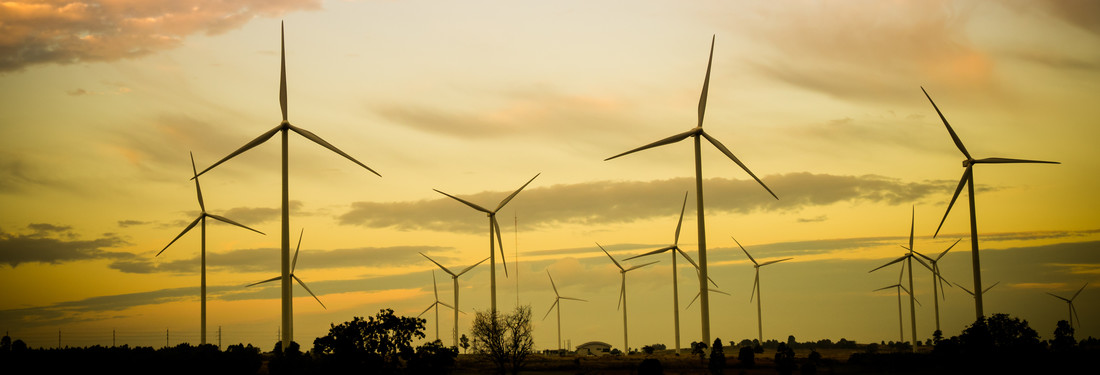
In the last decade, there has been much emphasis on carbon footprint reduction in new infrastructure projects as we need to meet sustainability goals and remain environmentally friendly with minimum carbon emissions. One way to reduce carbon emissions is to limit high-carbon energy sources and add a proxy price to carbon, as a result, bringing more transparency and traceability to the carbon supply chain in the project. Many countries, including the UK, have declared the Net Zero target by 2050 and attached a proxy price to carbon to curb carbon emissions and incentivise carbon offsetting technologies such as CCS (Carbon Capture and Storage).
In line with the 2050 Net Zero target, a public procurement policy announced by the UK government in 2021 mandated that all public contracts above £5m will require bidders to demonstrate how they will act to reduce carbon emissions. Bidders could get excluded if they fail to produce a satisfactory carbon management plan. Clearly, Governments are looking for a commitment from contractors, designers and consultants towards achieving the Net Zero target. With economic values attached to carbon usage in projects, it is imperative that the carbon supply chain is quantified and monitored. Furthermore, carbon exposure must be reduced and offset as per the approved carbon management plan. So, how do project managers deal with carbon management which is a relatively new area?
With carbon as a proxy for cost, we must exercise a multidisciplinary approach to get a bigger picture of the project’s carbon footprint by applying life cycle assessment (LCA) tools and quantifying it. As project professionals, we should explore and collaborate with technology partners to select energy-efficient technologies and, where possible, use low-carbon energy options. Although carbon management is complex and multi-disciplinary, the below steps, based on the carbon management hierarchy proposed by Bill Burtis and Iain Watt*, could come in handy for project managers working on new infrastructure projects.
Step one: carbon assessment
‘Total carbon footprint’ is an assessment of the direct and indirect carbon emissions from products or services over the complete project life cycle (construction, commissioning and operation). The life cycle assessment tool examines environmental impacts covering the entire supply chain from raw material procurement, transportation, processing to finished product, including storage, transportation, refluent disposal and end-of-life treatment. LCA starts after defining the LCA boundary and assessment scope. It aims to quantify the environmental impact of carbon emissions and carbon-intensive material inflow and outflow. LCA is usually carried out by sustainability consultants using LCA software tools. The assessment report provides a breakdown of the complete carbon footprint into small pockets covering the entire carbon supply chain in the project. It assists project managers in making informed decisions to select the most appropriate next step to avoid high carbon intensity in a particular pocket.
Step two: carbon reduction
Carbon reduction requires a multi-dimensional approach that includes procuring low-embodied energy materials, designing facilities with energy recycling processes and selecting energy efficiency measures. Embodied energy is the energy associated with manufacturing material that includes extracting and processing raw material, assembly and transportation. Embodied energy data of materials can provide important information about choosing them from a wide range of available options to lower indirect carbon emissions. However, direct carbon emission can be reduced by designing the energy recycling process. Energy recycling is about recovering heat or energy that would typically be wasted in industrial processes or released into the atmosphere; the recycling process allows recovered heat to be used in secondary heating processes or energy to operate low power equipment. Selecting energy-efficient technologies is another way to reduce direct carbon emissions. Energy efficiency is about consuming less energy to get the same amount of work with the help of innovative design and technologies. Project managers must collaborate with technology partners to explore energy efficiency options.
Step three: carbon replacement
Large infrastructure projects typically require substantial energy; the energy demand can be reduced but not eliminated. The next step in carbon management strategy could be replacing high carbon energy sources with onsite renewable energy generation. Onsite renewable energy sources cover heat pumps (underground or air sources), solar panels and anaerobic digestion units to produce biogas from waste. The energy produced from onsite renewable sources can be consumed locally earning green carbon credits for the new facility. With the cost of renewable energy generated from solar panels falling against the cost of electricity generated from conventional fossil fuels, onsite energy generation can also reduce energy bills on a long-term basis.
Step four: carbon offsetting
Carbon offsetting is about compensating direct or indirect carbon emissions to the environment with the help of natural or engineered carbon sinks. The carbon offset is the act of counterbalancing and therefore considered as the last option. Vertical gardening or on-plot farming could be one way to develop a natural carbon sink, however the adequacy of natural sinks depends on the emissions quantity released to the environment. Engineered sinks such as CCS are the preferred choice in industrial setups. Still, the economic viability of engineered sinks depends on the scale of operation and prevailing carbon price in the market. CCS technologies are still evolving and require substantial capital investment and strategic technology partners to develop an engineered solution. Hence, project managers must be aware of the complexity of developing carbon offset measures. We must focus on steps related to carbon reduction and replacement initiatives.
*Burtis, B. and Watt, I. (2008) “Getting to Zero: Defining Corporate Carbon Neutrality”, Clean Air-Cool Planet and Forum for the Future, Portsmouth, NH.
You may also be interested in:
0 comments
Log in to post a comment, or create an account if you don't have one already.