Crossrail: how prototyping led to assured outcomes and programme efficiencies
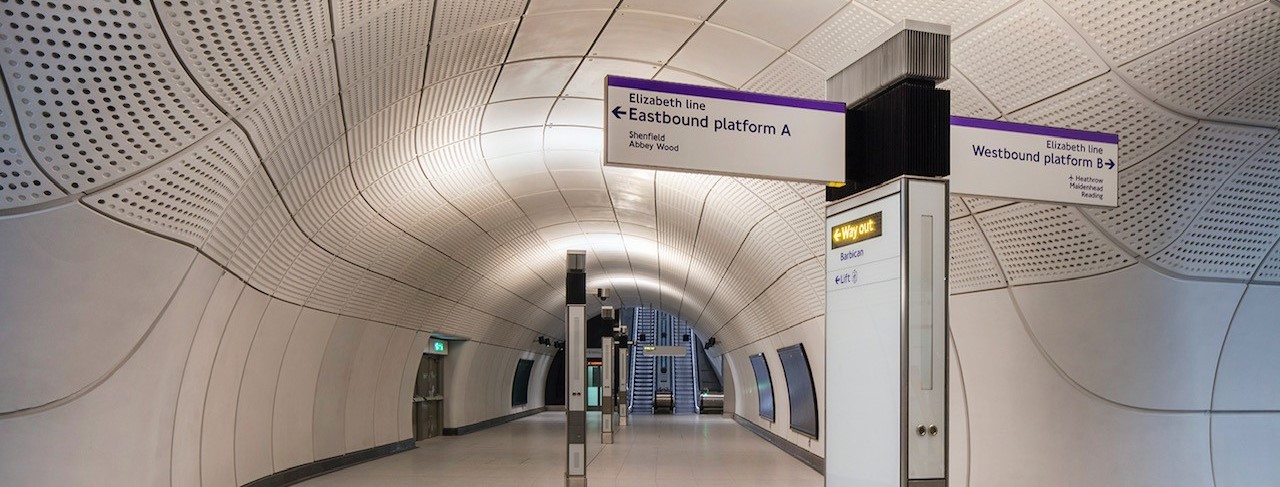
Many complex construction projects suffer setbacks because of unexpected problems that arise during production and installation, and ill-defined requirements upfront. On the £19bn Crossrail project, extensive physical prototyping was used as part of a project controls regime, reducing risks and assuring outcomes throughout the design development, procurement and construction phases.
For example, curved glass fibre reinforced concrete (GFRC) panels line the central London station tunnels. This material outperforms most others, but was relatively new to London Underground, so its use required extensive engagement to satisfy its technical performance and maintenance requirements over the project’s baseline design life of 120 years. The sheer quantity required (more than 50,000m2) meant that the risk of delivery and installation issues, and cost, needed to be well managed.
Outcome definition
The overarching project aim for Crossrail is to deliver a safe, operable and maintainable railway. Breaking this down, this means that the GFRC cladding needs to undergo an inspection and maintenance regime that can be undertaken during the times the railway is not in use, otherwise known as ‘engineering hours’. The working requirement for the designer was set against this defined outcome: panels would need to be inspected and maintained during this short window, as opposed to shutting the whole station down.
As the cladding was new to the operator, defining the required outcomes for it became a journey of demonstration and evidence. A key takeaway here for project managers, programme managers and those with complex portfolios is to plan for the management of risk in the areas of ambiguity and uncertainty. It was only once the requirements were clearly understood to achieve the desired outcome that risks could be either mitigated or transferred to the supply chain.
Key lesson: The example of maintenance shows how overall project requirements need to be translated into tangible desired outcomes involving stakeholders and operators.
The requirements outcome model and prototyping process
It became necessary to build a requirements outcome model, to be accepted by London Underground and then tested against by contractor teams and the supply chain.
Essential to this was the construction of a physical prototype by the client. The prototype was able to demonstrate how requirements could be achieved, for example its acoustic performance in relation to material and the size of acoustic perforations or, as mentioned, the maintenance regime of accessing panels in a limited time through time trials. In turn, this process avoided any asymmetries with respect to design information that the contractor teams would use to build their own prototypes as part of the client’s acceptance criteria.
Using the construction of a physical prototype and specific limited testing to establish requirements is a relevant model for any complex, safety-critical project. Examples could be in the transport sector, but also in energy and healthcare, and any large project involving construction.
Key lesson: Many projects will benefit from physical prototype requirement testing on the client side, engaging stakeholders and operators for project definition buy-in and significantly mitigating volatility and uncertainty risks to the project.
What requirements provided the outcome?
It was incumbent upon each contractor supply team to demonstrate that technical requirements could be met by each building their own full-size GFRC prototype. In total, three contactor prototypes were built.
Technical assurance could be achieved for the operator: giving confidence through testing on the prototypes that panels could be mounted and de-mounted in constrained time windows. Using these prototypes, the requirements outcome could be further checked and verified accordingly. Within a developmental window of over a year, the contractor’s supply chain teams could begin to benchmark the quality of the GFRC panels themselves.
Some explored a route of spraying the panels with metal inserts to optimise material use, while others explored pouring high-performance concrete into adjustable moulds. Commercial imperatives existed for each design and build contractor team as they sought to produce prototype artefacts that would emulate the client’s desired outcome model. It was clear that the acceptance criteria would be tested against the client’s outcome model; the model consisted of drawings produced by the client’s designer, specifications as well as the ongoing acceptance criteria of London Underground. On each contractor prototype, the access, maintenance and inspection regimes of the operator were simultaneously developed and qualified.
Key lesson: Ensure sufficient time is allowed for the supply chain to undergo development and emulation of the client’s desired outcome.
Supply chain procurement
Handing over consistent, clear information to the supply chain is the last stage in this outcome realisation process. The steps above allowed symmetric information to be given to the supply chain, hence risk was in turn mitigated (with nowhere to delay, hide or cheat!). Having undergone an outcome model and process where the design of the GFRC panels had been made and tested through the client prototype, a successful gateway had been achieved. This says: ‘Yes, the outcome the client is intending to achieve is possible in certain terms.’ In turn, it said that it was going to be possible to procure for what is known to be certain. In simplistic terms: you don’t know what you want until you have made it.
Having determined that the outcome could be realised, the last aspects of progressive assurance could be undertaken: simply ensuring each of the three supply chain prototypes produced would evidentially meet London Underground’s access, maintenance and inspection needs. This closed the last stages of progressive assurance from delivery to handover. For the contractors, the prototyping allowed them to optimise their production methods (saving millions in the optimisation of geometries and reduction of waste) and test their installation before coming to site, benefits often associated with MMC (Modern Methods of Construction).
Although physical prototyping may initially appear costly and time-consuming, these benefits weigh up. David Shillito, director of GFRUK (a Laing O’Rourke company), remarked: “It was absolute agony, but it was worth its weight in gold. If you take away one lesson – don’t ever take away a prototype requirement for a project of that scale. It is absolutely essential. If we had not constructed a prototype, it would have been a disaster.”
You may also be interested in
- Crossrail chairman Tony Meggs on the challenges of megaprojects
- Reading the latest news in Project journal
- Exploring project management resources
Image: Morley von Sternberg
This blog is co-written by Jim Abatti and Jorrin ten Have.
Jorrin ten Have is an architect and associate principal within the international architecture practice Grimshaw. Jorrin has led the line-wide design team as project architect since the start of contractor involvement to construction and installation on-site. As part of this role, he was extensively involved in the detailed development and prototyping process of the GFRC systems and advised Crossrail on their acceptance of the contractor’s designs.
0 comments
Log in to post a comment, or create an account if you don't have one already.